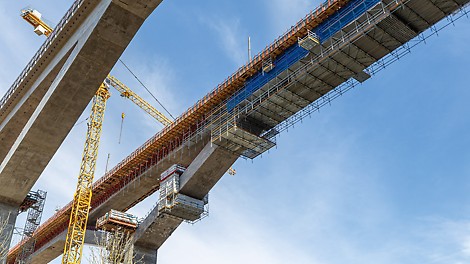
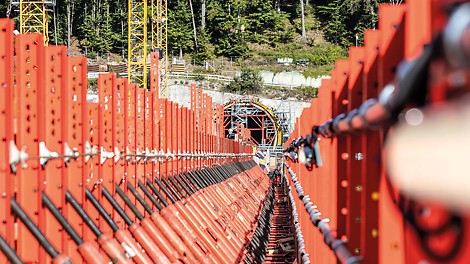
Download Press Release
The images in more detail
The 485 m long Filstal Bridge is part of the new high-speed Wendlingen-Ulm railway line. At a height of 85 m, it is one of the highest railway bridges in Germany, connecting the Boßler Tunnel in the north with the Steinbühl Tunnel in the south. As the tracks run on two separate bridge sections, the structure is extremely demanding in terms of architecture and engineering.
Solution provider
The Filstal Bridge brings together all the challenges of bridge construction: high bridge piers that widen in a Y-shape at the crown, a sophisticated construction method with slender superstructures, high architectural concrete requirements and a narrow time window to meet the completion deadline because of interim adjustments to the structural model of the bridge structure. In PERI, an experienced solution provider for formwork and scaffolding projects was on hand to support the construction consortium partners, Max Bögl and PORR. Particularly when requirements changed during the construction process, the infrastructure specialists always found a solution to meet the completion deadline and at the same time achieve a high quality of execution. In all phases, digital 3D planning provided visualisations of the formwork and scaffolding use, thus simplifying communication with the various decision-makers.
Pier construction kit
Three PERI modular systems served as the formwork and scaffolding basis for the bridge pier construction work. The slender reinforced concrete shafts sprouted upwards, cycle by cycle, with the aid of the rail-guided RCS climbing formwork. In the complicated expansion areas at the pier head, working platforms based on the RCS and SCS climbing systems ensured that the loads could be transferred safely. For this, PERI UP reinforcement scaffolds installed around the perimeter provided a safe working environment.
Y-pier special feature
The way in which the inclined piers between the Y-pier head and the superstructure were worked on was a special feature of the project. For this purpose, PERI engineers designed a rail-guided finishing carriage by combining the PERI UP Scaffolding System with VARIOKIT and RCS climbing technology. This allowed the entire scaffolding unit to be moved hydraulically in 50-cm-increments to the desired position, guided safely via RCS Climbing Rails and Shoes on the inclined pier caps and connected to the structure.
Combination solutions for the superstructure
The two single-track superstructures running parallel to each other were constructed as pre-stressed concrete end-to-end girders using a formwork carriage – first the west bridge, then the east bridge. The cantilevered parapets on the west bridge were constructed in 24-m-sections using a total of four VARIOKIT Cantilevered Parapet Carriages. The VARIOKIT carriages were then fitted with additional PERI UP scaffold suspensions and could then also be used for quality-assuring finishing work. At the same time, the PERI solution could be used as assembly scaffolding for the windbreak wall by adding additional scaffolding and enclosing it as required as wind and weather protection.
In order to speed up the construction process considerably, the working platforms on the eastern superstructure were kept available along the entire length of the bridge so that the parapet could be constructed in sections. The project-specific VARIOKIT solution from the PERI engineers also took the additional assembly and finishing platform applications into consideration here. The metric basic grid of both modular systems, VARIOKIT and PERI UP, paved the way for an almost limitless number of combinations in all respects, which was hugely beneficial for planning, structural analysis and on-site construction work. For this, the consortium partners Max Bögl and PORR had a competent subcontractor at their side in Schäfer Gerüstbau, who had already had positive experiences with both PERI systems while carrying out assembly work on countless construction sites. With safe, coordinated work processes, the agreed deadlines could be met without any interruptions that might delay construction. The high level of working safety facilitated both the formwork and scaffold assembly processes as well as subsequent use at great heights and in the area of the motorway crossing at the Drackensteiner Hang on the A8.
The impressive versatility of the PERI UP Scaffolding Kit meant that the suspended scaffolds could be optimally adapted to the geometry of the bridge. Using the new, second generation of PERI UP components also resulted in noticeable weight advantages and increased the load-bearing capacity by, for example, enabling the standards to be double-pinned. In addition, the modular, easy-to-handle system formwork girder could be used to quickly and easily install bridging in 25-cm-increments up to a length of 10 m – without tubes and couplings.
Tunnel portals
The comprehensive service package provided by PERI comprising engineering services, construction site support, chief erectors and factory pre-assembly even included the final construction of the tunnel portals as a transition between the bridge and the tunnel. As the tunnel formwork carriage was also based on the VARIOKIT Engineering Construction Kit with rentable system components, it was possible to develop a customised project solution, deliver it to the construction site and assemble it on site in no time at all. Both large-format recesses for sound propagation and sections that had to be formed and concreted on one side were taken into account.